LIFE CYCLE SERVICE
MARINE FIELD
Keeping ships healthy anywhere in the world
like a “ship’s electrical doctor” should
NEW SHIP
New Ships
Servicing Support
Tasked with providing servicing support during new ship construction and product warranty periods
Teratec provides meticulous servicing support for products supplied to customers by our parent company Terasaki Electric Co., Ltd. As their engineering wing, we swiftly respond to specification changes during the construction process and any problems that arise during the product warranty period (1 year unless otherwise specified). We also report customer demands and improvement work to Terasaki, which they use to hone technologies and enhance the quality of their marine systems and breakers.
Major locations where we operate
- Japan
- Shipyards around the world
Field Work
- System commissioning
- As the first step to ensuring ship electrical plants and systems operate safely, we carefully check that equipment has been installed and wired as per drawings and diagrams, and operates as intended.
- Performance testing
- We carefully check that important protective, control and monitoring systems and equipment operate correctly and assuredly in the actual onboard environment.
- Test-runs and tuning
- We carefully monitor and tune equipment operating status during system test-runs,
- Training in operation and handling
- We explain the technical fundamentals and operating procedures of onboard electrical plants and systems to shipyard builders and ship crews. These training tutorials assist the customer in their work safety efforts by laying out example scenarios of potential and unlikely troubles, and highlighting the dangers of human error. The content of the tutorials can be tailored to customer request.
- Improvement work related to specification changes
- It can happen that specifications are changed before plant/system commissioning because of equipment size and quantity increases. We devise the best way to swiftly and properly perform the improvement work without impacting the shipbuilding process.
IN SERVICE SHIP
In-Service Ships
Technical Service
Wide-ranging continuous technical services for ship electrical plants and systems from delivery to discard
We provide customers with technical services for their ship’s electrical plants and systems across the full lifecycle of the equipment from commissioning to decommissioning.
Major locations where we operate
- Japan
- Shipyards around the world
- Ports around the world
Basic Maintenance Plan Proposals
- We propose checks and maintenance plans for important equipment and systems according to the number of years they have been in service. (We additionally scrutinize consumable parts and include a parts replacement plan if needed.)
- Final drawings and documents of the delivered equipment, specifications of important equipment and systems, and work history reports including records of parts replacement are centrally managed on a database and used to support the customer in their efforts to maintain and manage equipment over its full lifecycle.
- Equipment and system integrity are diagnosed using checklists that are created from equipment field data and inspection records.
- We welcome consultation requests regarding checks and maintenance of medium voltage equipment and relays of other manufacture.
Lifecycle Technical Support Proposals
- We can propose viable periods for prolonging equipment updates based on the number of years of continuous maintenance performed on equipment and systems, the number of years that equipment has been in service, and customer budgets.
- We can support improvements in functions by updating to the latest equipment / systems and quickly response to latest technologies.
- Work plans for equipment updates are formulated in consideration of foreseeable restrictions (duration of system downtime, work performed during ship operation, etc.).
- We will also explore the possibility of updating unserviceable or discontinued equipment and systems of other manufacture with products by Terasaki Electric, and build workable proposals.
We can offer customers total solutions that bundle contracting, equipment design and field servicing into a single package.
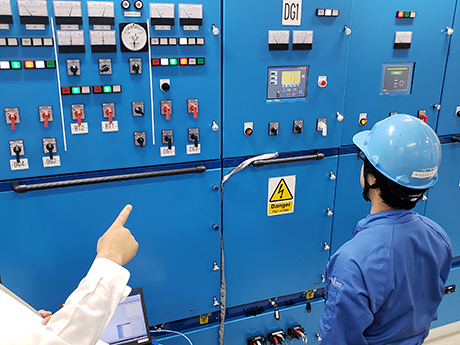
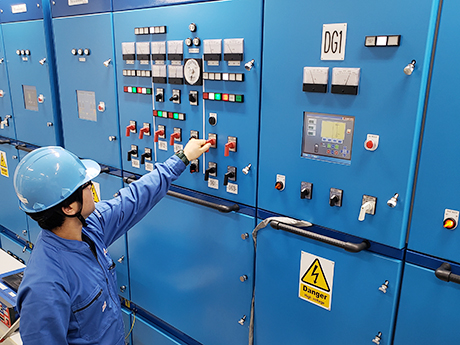
In-Service Ships
Maintenance
Making full use of sensorial perception,
data and tools in maintenance
Maintenance work for ship electrical equipment, plants and systems is mainly classified into “status monitoring” and “scheduled” maintenance. Both are forms of preventative maintenance. This former relies on the ship operator monitoring the status of operating equipment and systems when it cannot be stopped or powered down (e.g., at sea, anchorage, etc.), while this latter is performed at a predetermined time (schedule), which allows equipment and systems to be stopped or powered down for detailed inspections and overhaul. At Teratec, we make full use of the sensorial perception we have honed over the years, data and tools to perform maintenance to the customer’s wishes.
Major locations where we operate
- Japan
- Shipyards around the world
- Ports around the world
Checks & Servicing
- We utilize a database of ship-specific information to accurately perform checks and servicing.
- For each and every ship, a massive database of information (ship’s list) is built of the specifications of onboard equipment and systems, and records of checks, servicing, repairs and improvements. Then, highly seasoned servicemen use this data, technical know-how and management criteria from the equipment manufacturers to accurately check and service the ship’s equipment and systems.
- In addition to equipment checks and servicing aboard ship, we offer equipment overhauls that enhance running stability and prolong equipment service-life at our service shops.
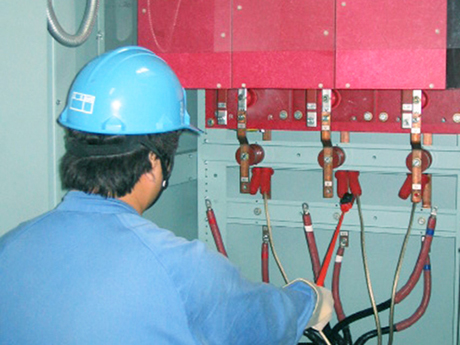
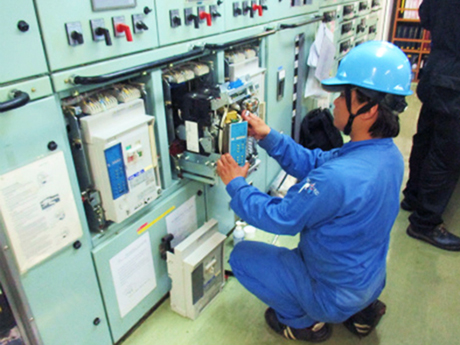
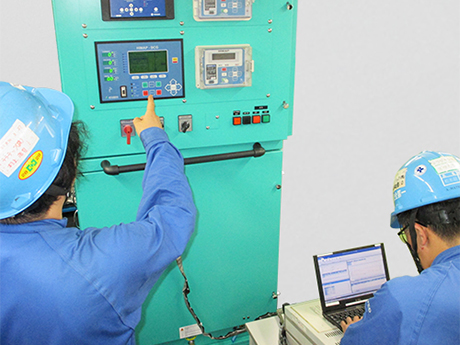
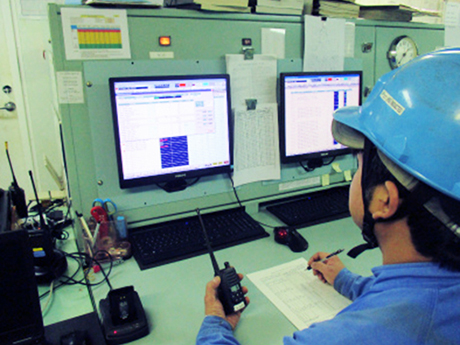
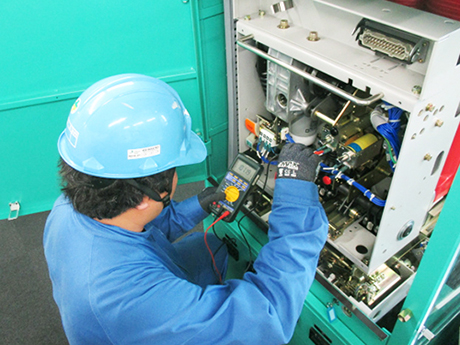
Repairs
- If equipment or systems break down, we restore operation and performance by replacing or retuning electrical and mechanical parts, using the latest optimization technologies.
- By having Teratec check and service equipment and systems aboard ship or overhaul equipment at one of our service shops, customers can expect enhanced stability and longer service-lives.
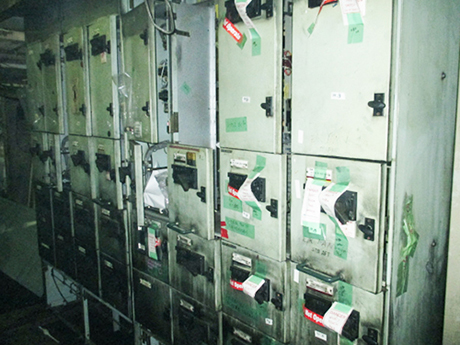
Before
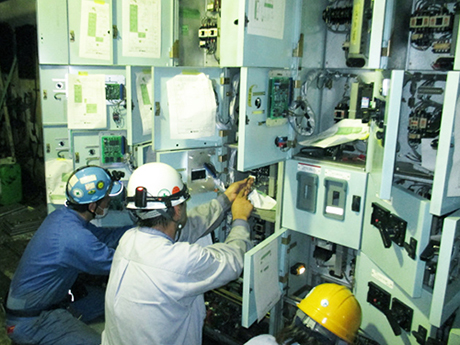
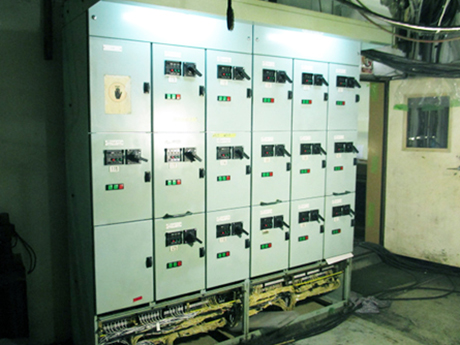
After
Analysis & Diagnosis
- Use of thermographic imagery
- Conventional maintenance is performed with the target equipment powered down, but some troubles can only be detected with circuits in the live state. We, therefore, introduced thermographic analysis and diagnosis in order to reduce the risks of unexpected trouble.
Thermographic image of the terminals of an air circuit breaker (ACB) seen from the rear
- Analysis of current flows by digital data recorder
- Our service teams use the latest digital data recorders that reproduce voltages, current flows and signals as visible waveforms, to project current flows inside of equipment as numbers and graphs from which aging and deterioration can be analyzed.
-
Specification Changes & Improvements
- Electrical plant upgrades and changes to environmental regulations placed on ships can trigger necessary specification changes for onboard electrical distribution, control and monitoring equipment and systems. Teratec can swiftly make the required improvements at ports of call and repair docks around the world, by putting together the best work method and flow for the job.
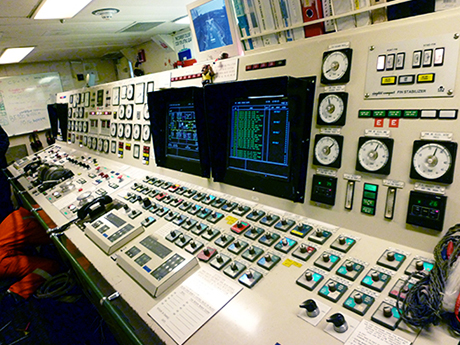
Before
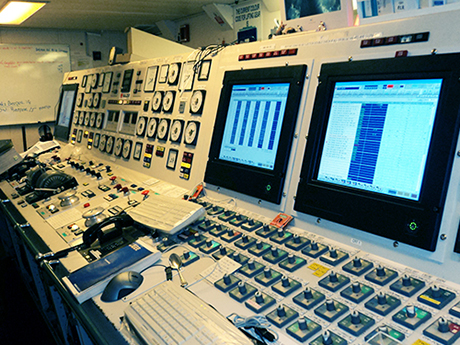
After
In-Service Ships
troubleshooting
Scrambled support for trouble at sea
If a ship at sea incurs trouble in its electrical distribution and control equipment or systems, we scramble our support teams. Right from the get-go, the sales, design, field support and quality assurance departments at Teratec work as one to repair and restore equipment to guaranteed levels of safety and performance. If trouble occurs at a port of call or shipyard in Japan or somewhere around the world, service teams from our offices or members of the TEAM TERASAKI Global Service Network race to the site in order to repair and restore equipment in the least amount of time possible.
Major locations where we operate
- Japan
- Shipyards around the world
- Ports around the world
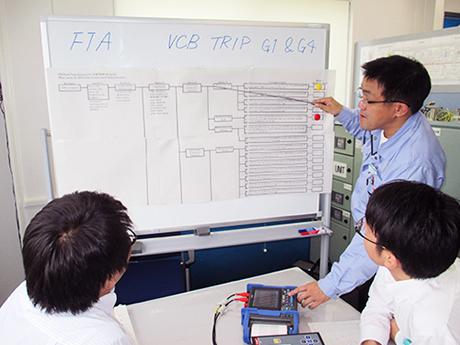
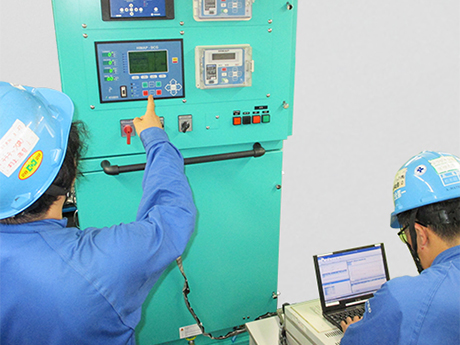
Troubleshooting workflow
In-Service Ships
Environmental Compliance & Energy-Savings Support for Ships
Improvement work for environmental compliance
In recent years, Teratec has been doing improvement work on in-service ships to ensure their compliance with maritime environmental regulations, as a collaborative effort with shipyards and onboard equipment manufacturers,
Workflow for installing a ballast water treatment plant and improvements for emissions gas regulatory compliance
STEP.01
Preliminary discussions & Estimate request
Prior to any explaining or meetings, we ask the customer to provide us with the specifications and photos of the target equipment.
Teratec (Sales, Engineering, Service)
Preparation of an improvement work plan
We explore ways to improve the target equipment and systems, based on the information provided by the customer.
・Confirmation with the rule of Classification society
Confirmation of existing switchboards (Short circuit current, Busbar capacity)
Ship inspection, preparation of basic drawings (draft), selection of the best equipment/materials
Extraction of field risks, calculation of work period and man-hours
Determination (necessary/not necessary) and calculation of power downtime, preparation of requests for the customer
- Improvement work plan
- Estimated price, work period, man-hours, best workflow, verification testing considerations, work requests for other contractors, summary of requested items, etc.
STEP.02
Prior to an order being placed
We submit an “Improvement Work Plan” to the customer.
Meeting with the customer and other companies (engineering companies, shipyard, etc.) involved in the project (To discuss the suitability of the Improvement Work Plan)
STEP.03
Once the job is ordered
We proceed with planning and verifying the details, and procuring parts/materials.
Teratec (Sales, Engineering, Service)
Preparation of detailed designs (Shop drawings, changes to as-completed drawings)
Finalization of improvement method (Efficiency, quality, risk avoidance)
Procurement of equipment/materials
Finalization of improvement workflow (Time frame, personnel, layout, etc.)
Finalization of field test method
- Work Plan
- We prepare a “Work Plan” based on the customer’s desired schedule and submit it to the customer.
STEP.04
Work start
After obtaining the customer’s approval of the Work Plan, we start work at the designated location.
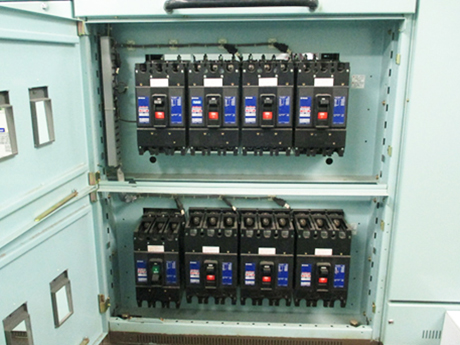
Before
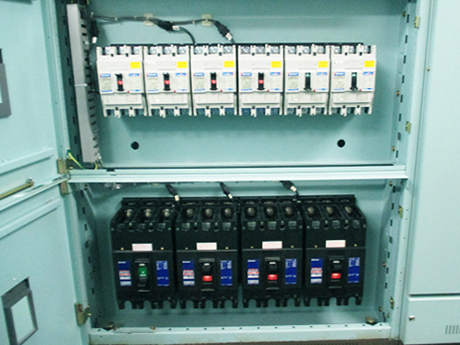
After